Blog
the challenges and solutions in importing raw materials for the construction industry
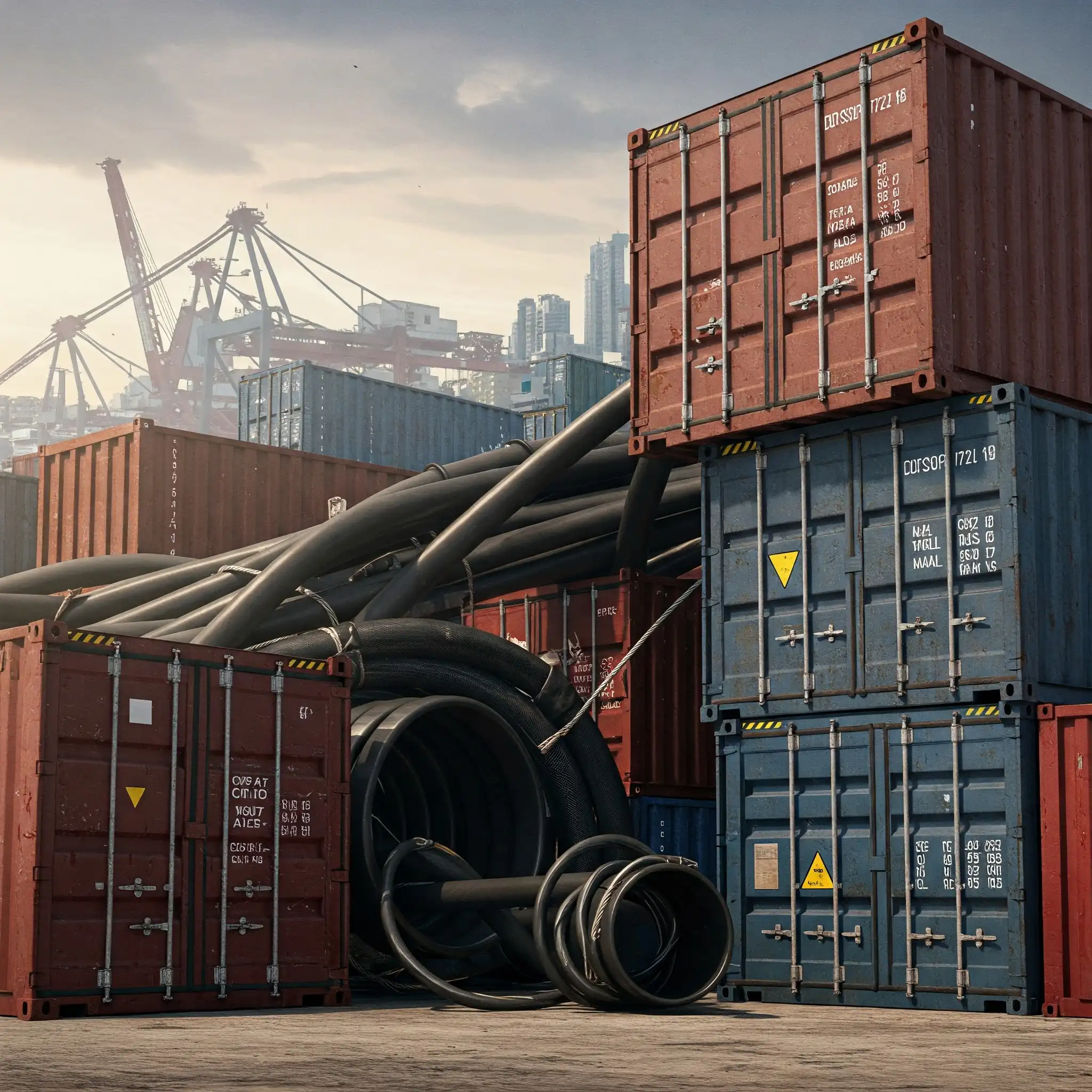
The global construction industry is heavily dependent on the import of various raw materials, from basic materials such as cement and steel to specialized components such as advanced plumbing equipment and unique exterior cladding. The import process is complex and exposed to a number of significant challenges that can affect project costs, schedules and even the quality of construction. This article will examine the main challenges in importing raw materials for the construction industry and offer possible solutions to deal with them, while addressing the importance of supply chain management for companies like Mano Group.
Raw material price volatility
One of the most prominent challenges is the high volatility in raw material prices in global markets. Factors such as changes in demand and supply, geopolitical conditions, natural disasters and international trade policies can lead to sharp price increases and instability.
Impact: Unexpected price increases may significantly increase construction costs, harm project profitability and delay their start or completion. Price volatility makes it difficult for contractors and developers to plan accurate budgets and manage their risks.
Solutions: Companies like Mano Group can diversify their import sources to reduce dependence on a single supplier or a specific geographic region. Managing financial risk through futures or options can help hedge against price increases. Building long-term relationships with reliable suppliers and managing inventory strategically can also contribute to price stability.
Disruptions in the Global Supply Chain
Global supply chains for building materials are complex and involve a large number of actors, from manufacturers and suppliers to shipping companies and ports. Disruptions at one point in the chain can lead to significant delays in the supply of raw materials.
Impact: Delays in supply can disrupt construction project schedules, lead to fines and additional costs, and in extreme cases, even stop work on site. Uncertainty about delivery dates makes it difficult to coordinate with contractors, suppliers, and other professionals.
Solutions: Mano Group can invest in building a more flexible and resilient supply chain. This includes working with multiple alternative suppliers, closely monitoring shipment status using digital technologies, and detailed logistics planning that takes into account potential risks. It may be worth exploring options for local production of some raw materials to reduce dependence on imports.
Freight and handling costs
International freight and handling costs constitute a significant portion of the total cost of imported raw materials. Factors such as fuel prices, shipping rates, port congestion, and changes in traffic regulations can affect these costs.
Impact: Increases in freight costs make imported raw materials more expensive and reduce their competitiveness against domestic materials. Port delays or logistical issues can lead to additional storage costs and impact project schedules.
Solutions: Mano Group can streamline its logistics processes by consolidating shipments, planning efficient transportation routes, and selecting reliable and efficient shipping companies. Using logistics management technologies can help track shipments and make informed decisions about transportation methods.
Differences in Standards and Regulations
Construction materials imported from different countries may be subject to standards and regulations that differ from those in the importing country. These differences can create difficulties in approving materials, require additional testing, and delay their use in projects.
Impact: Non-compliance with local standards can result in construction delays, additional costs for compliance or testing, and in severe cases, even disqualification of the materials. Understanding and adhering to the various regulations is essential to avoid these problems.
Solutions: Mano Group should conduct a thorough review of the relevant standards and regulations in the importing and destination countries. Working with suppliers who are familiar with local standards and using regulatory consulting services can help ensure compliance and avoid delays.
Geopolitical and trade policy risks
Political instability, international conflicts, and changes in trade policies, such as the imposition of tariffs or import restrictions, can significantly affect the availability and cost of imported raw materials.
Impact: Sanctions, trade wars, or sudden changes in tariff policies can disrupt supply chains and significantly increase the cost of imported raw materials, and in some cases even stop imports altogether.
Solutions: Companies like Mano Group should monitor geopolitical developments and international trade policies and analyze their potential impact on their import activities. Diversifying import sources and preparing for different scenarios can help reduce risks.
Effectively dealing with the challenges of importing raw materials is critical to the success of construction projects and maintaining competitiveness in the industry. By implementing strategic solutions, intelligent risk management, and investing in building a strong and flexible supply chain, companies like Mano Group can reduce the negative effects of import challenges and ensure a regular and efficient supply of quality raw materials.